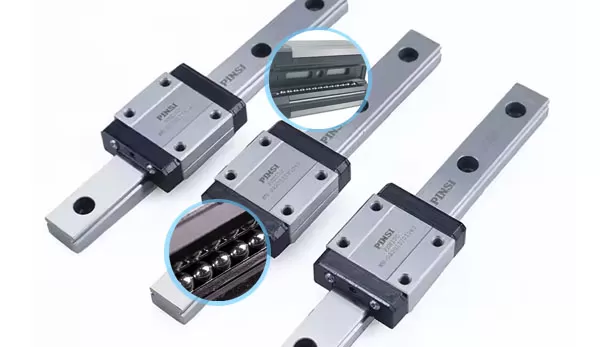
Following is a detailed comparison of steel, aluminum, and polymer as linear guide materials to help you make an informed choice.
Why material choice matters for linear guides (precision, load, environment, cost).
Overview of steel, aluminum, and polymer options.
● Steel Linear Guides
Pros:
Highest load capacity and rigidity.
Superior durability and long lifespan.
Resistant to wear and deformation.
Cons:
Heavier, increasing machine weight.
Prone to corrosion (unless stainless or coated).
Higher cost for hardened/precision grades.
Best For:
CNC machines, heavy industrial equipment, high-force applications.
● Aluminum Linear Guides
Pros:
Lightweight (ideal for high-speed applications).
Naturally corrosion-resistant.
Easier to machine/modify.
Lower cost than precision steel.
Cons:
Lower load capacity vs. steel.
Less rigid (may flex under heavy loads).
Best For:
Robotics, 3D printers, medical devices, cleanroom environments.
● Polymer/Composite Linear Guides
Pros:
Lightweight and corrosion-proof.
Self-lubricating (maintenance-free).
Quieter operation (vibration damping).
Cost-effective for low/medium loads.
Cons:
Lower temperature resistance.
Not suitable for heavy loads or high speeds.
Best For:
Food processing, packaging, lab equipment, washdown environments.
By evaluating your application's load, precision, environment, and cost constraints, you can select the optimal linear guide material or explore composite solutions for performance optimization.